Sewing Machine Repair
Our dedicated service team is here for all your Bernina, bernette, Janome, Juki, Baby Lock, APQS, and Handi Quilter machines. Always ahead of the curve with the newest techniques, we ensure your prized machines get the top-notch care they deserve. Experience exceptional service marked by prompt returns and open communication every step of the way. Should any unexpected repairs arise, rest assured we'll promptly update you with a detailed quote before moving forward.
Our Technicians
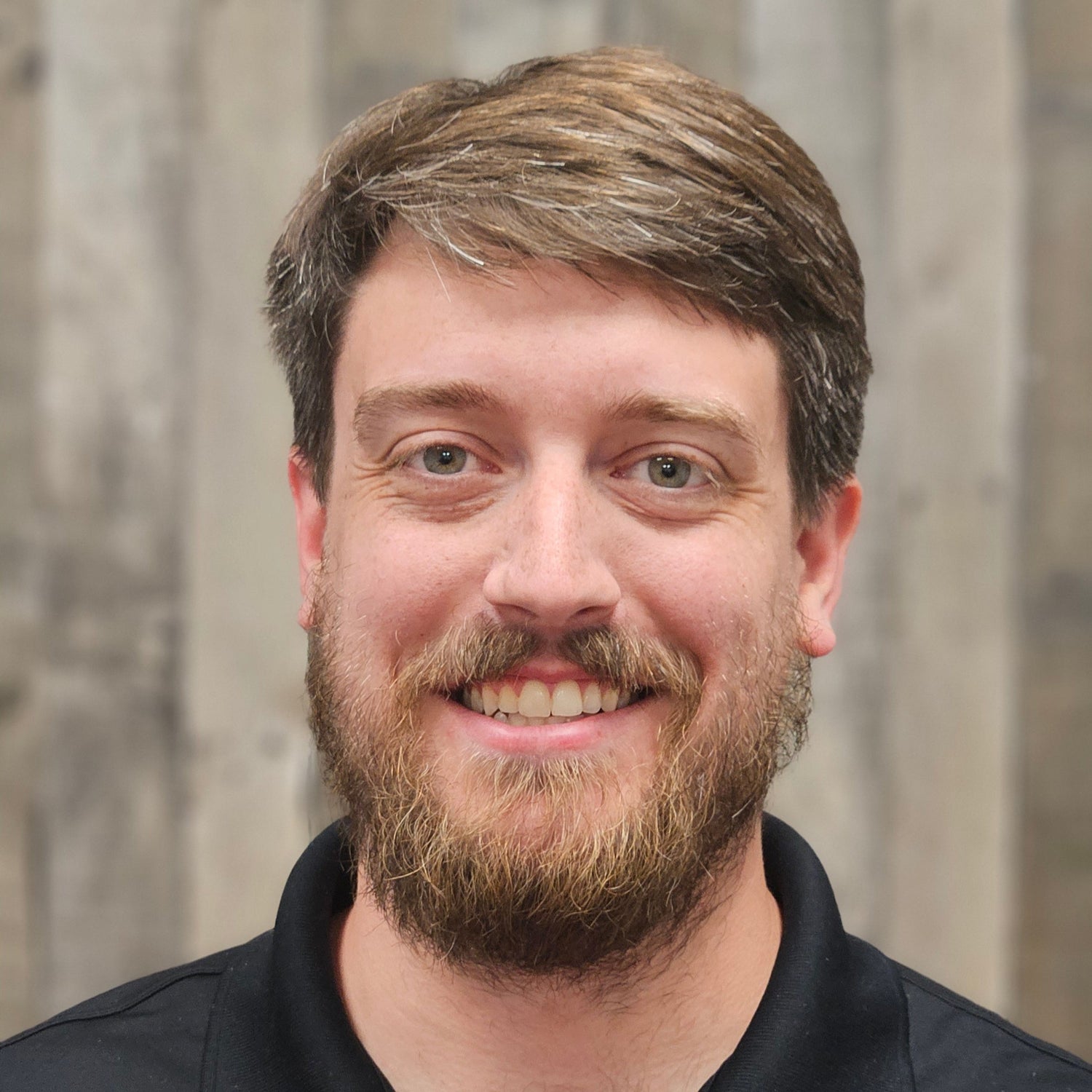
Jacob aka Jake
Jacob brings expertise, dedication, and a passion for precision to his role as Owner and Head of Repair. Certified in Bernina, bernette, Janome, Baby Lock, Juki, APQS, and Handi Quilter repair, he has honed his skills to ensure every machine he works on receives the highest standard of care. His exceptional attention to detail and patient approach make him a trusted problem solver for both colleagues and customers.
Jacob thrives on helping others, fueled by a steadfast commitment to providing solutions that keep machines running smoothly. It's his belief that trust is built through consistency, and he takes pride in delivering top-notch service every day.
When he’s not busy repairing machines, Jacob enjoys raising his family and cherishing the moments they share. He’s currently learning the intricacies of golf, appreciating the patience and focus it requires. Known for his love of the 4th of July, Jacob delights in setting off fireworks and celebrating the holiday with his family.
Approachable, experienced, and driven by a passion for his craft, Jacob is at the heart of everything his business stands for.
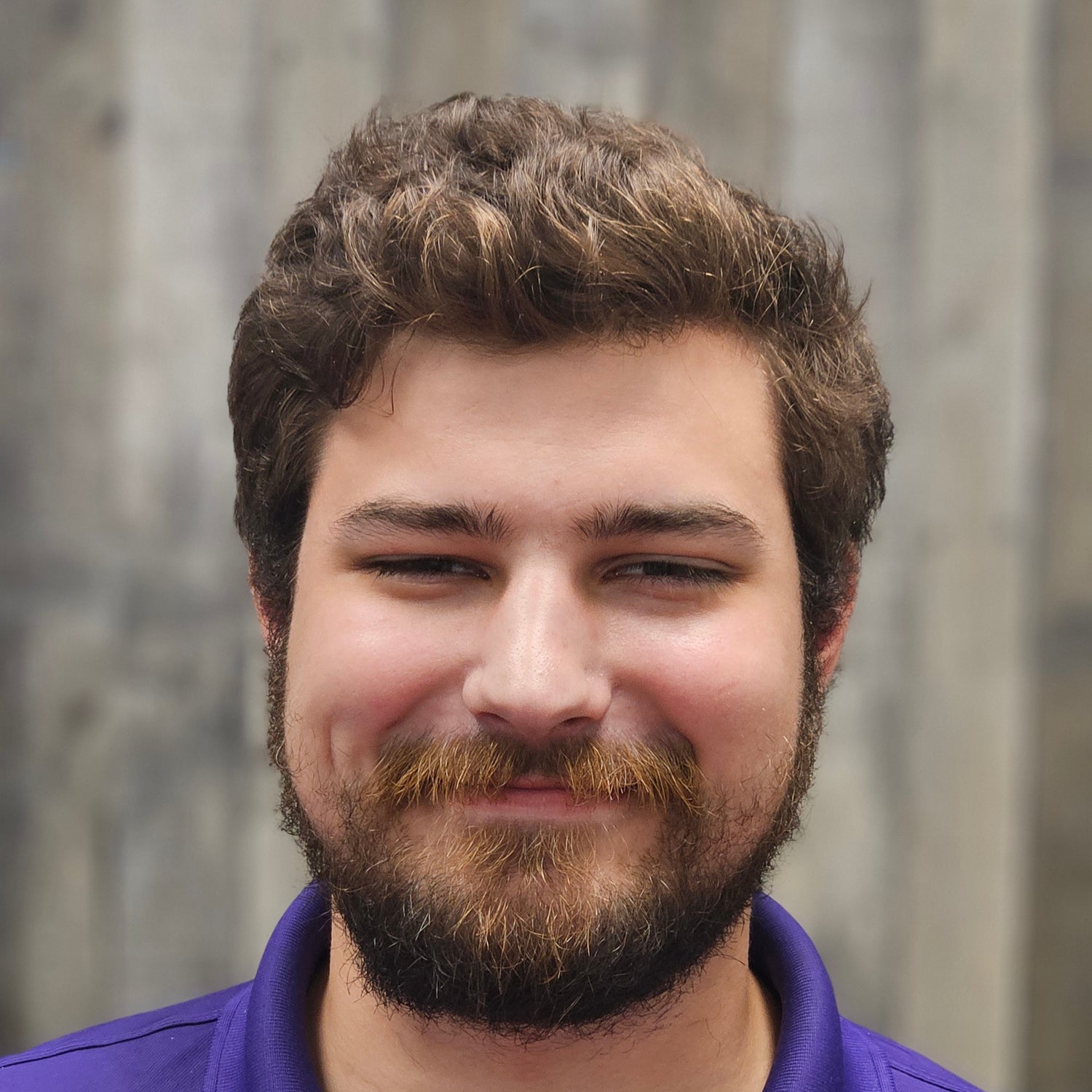
Greg
Greg joined our team in 2024 and quickly became an integral part of our operations. A natural problem-solver with a hands-on approach, Greg thrives on tackling challenges and getting machines back in top working order. His favorite equipment to work on? Longarms. Their complexity and precision are right up his alley, making them his specialty.
Known for his energetic, can-do attitude, Greg is always on the move, eager to learn and take on new tasks. His quick adaptability and dedication to his craft ensure that no problem is too big or too small for him to handle.
Outside of work, Greg has a heart for the community. He spends his spare time giving back, helping others whenever and wherever he can. This passion for supporting people—both on and off the job—makes him a valued team member and an inspiration to those around him.
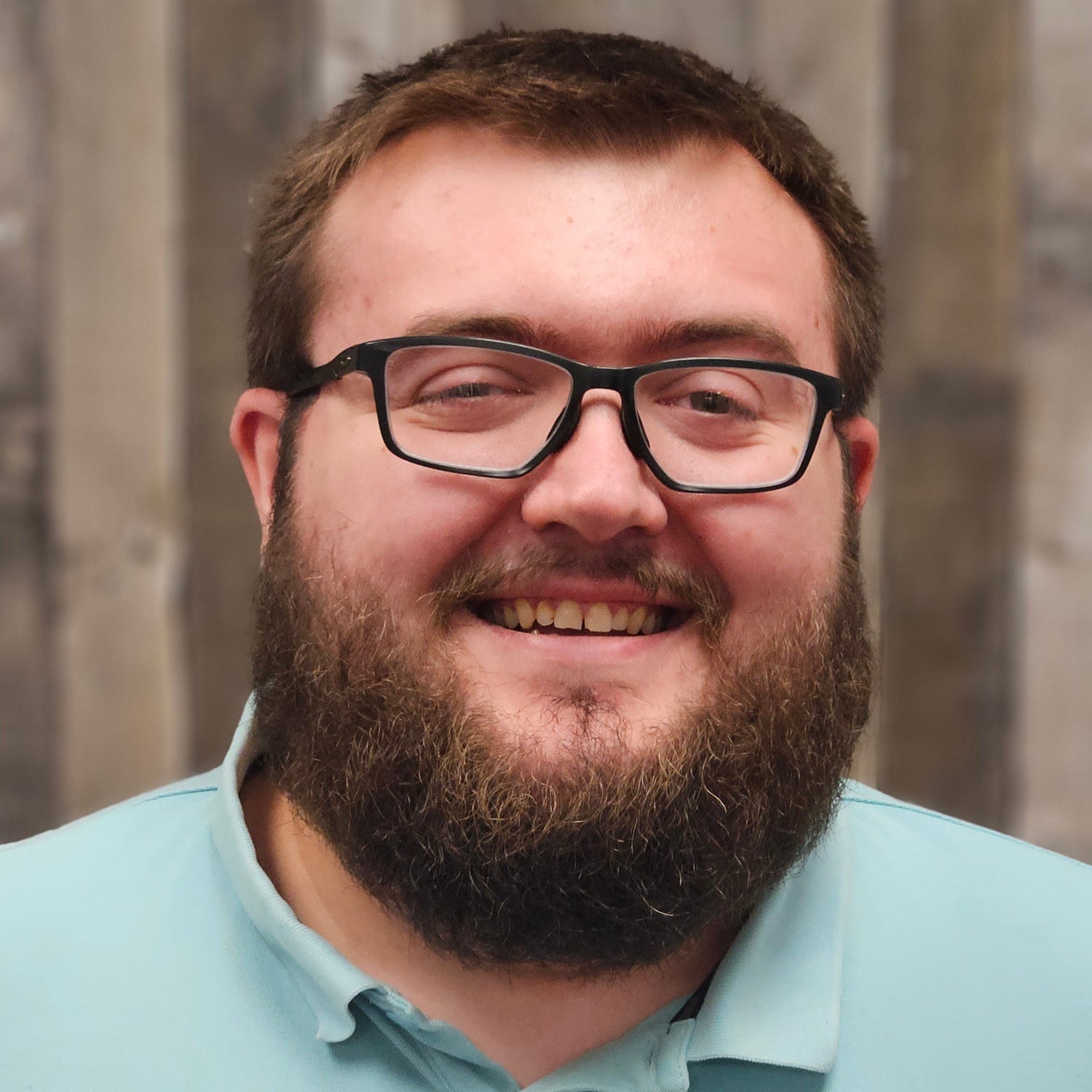
Tyler
We’re excited to welcome Tyler to the Fabric Bash Technician team as our newest Repair Technician! Tyler brings a hands-on approach to his work, complemented by a genuine curiosity for how things function. With a passion for building computers and an enthusiasm for taking things apart to see how they’re made, Tyler’s knack for problem-solving makes him a great addition to our team.
Eager to connect with our customers, Tyler looks forward to providing support and expert care for their sewing machines. His warm and approachable demeanor, combined with his technical expertise, ensures that every customer feels confident and well-taken-care-of.
Be sure to stop by and say hello – Tyler is ready to assist with all your sewing machine needs!
FAQs
Repair timelines can vary depending on the issue, but most cleanings are completed within 5-7 business days. Complex repairs might take longer, but we'll keep you updated throughout the process.
Yes, we tune up all brands of home sewing machines, including mechanical, electronic, and computerized models. If you're unsure about whether we can fix your machine, feel free to contact us with your machine's details.
Bring your machine in and it will be serviced in the order received.
When bringing your machine in, please include the power cord, foot pedal, and any accessories related to the issue (e.g., specific presser feet). This helps us test and repair your machine effectively. Also include any samples of the problem.
If you have further questions, don’t hesitate to get in touch! We’re here to help with all your sewing machine repair needs.
Regular upkeep helps extend your sewing machine’s life and keeps it running smoothly. Clean the bobbin area to remove lint, oil your machine as recommended in your manual, and replace needles regularly. Always use high-quality thread and store your machine in a dust-free environment when not in use.
Check out Greg's video by clicking on this link: https://youtu.be/5oeVHxjuEc0
Frequent problems include thread bunching, skipped stitches, and tension troubles. To troubleshoot, check for correct threading, ensure the needle isn’t bent or dull, and make sure you’re using the right bobbin. Many minor issues can be fixed by rethreading the machine, cleaning the bobbin case, or changing the needle.